You can see I had to make several runs in different gears to cover the whole RPM range.
then trace (yellow) the boost curve that emerges from the compiled runs.
logged runs from KFLDRAPP = 0
traced at same RPM points as KFLDRL in yellow (table below)


logged runs from KFLDRAPP = 10 (leaving lower 3 PED% rows =0)
traced at same RPM points as KFLDRL in yellow (table below)
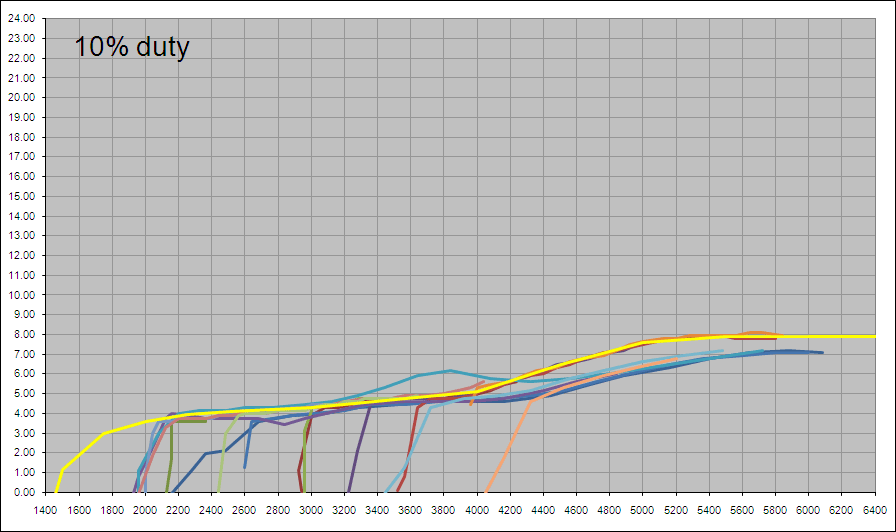

logged runs from KFLDRAPP = 20 (leaving lower 3 PED% rows =0)
traced at same RPM points as KFLDRL in yellow (table below)


logged runs from KFLDRAPP = 30 (leaving lower 3 PED% rows =0)
traced at same RPM points as KFLDRL in yellow (table below)

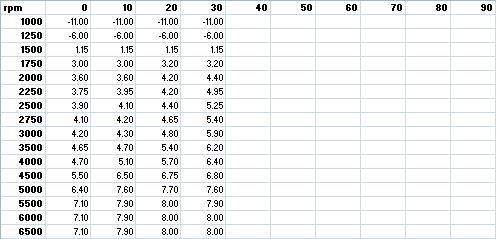
logged runs from KFLDRAPP = 40 (leaving lower 3 PED% rows =0)
traced at same RPM points as KFLDRL in yellow (table below)

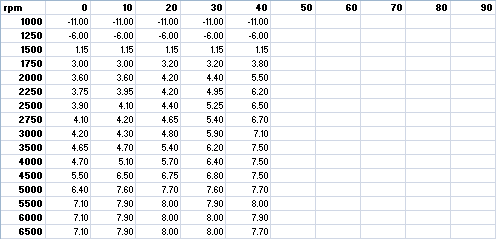
logged runs from KFLDRAPP = 50 (leaving lower 3 PED% rows =0)
traced at same RPM points as KFLDRL in yellow (table below)


logged runs from KFLDRAPP = 60 (leaving lower 3 PED% rows =0)
traced at same RPM points as KFLDRL in yellow (table below)
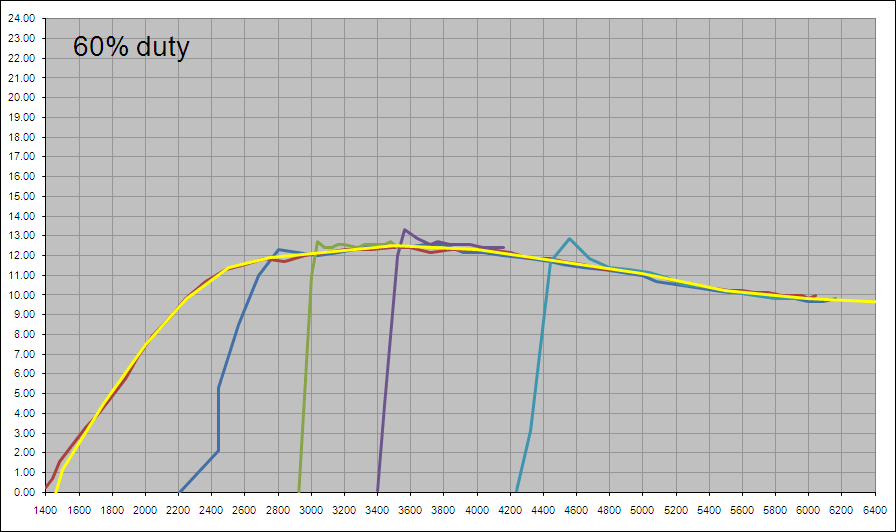

logged runs from KFLDRAPP = 70 (leaving lower 3 PED% rows =0)
traced at same RPM points as KFLDRL in yellow (table below)


logged runs from KFLDRAPP = 80 (leaving lower 3 PED% rows =0)
traced at same RPM points as KFLDRL in yellow (table below)

