nubcake
|
 |
« Reply #135 on: November 21, 2016, 10:08:23 AM »
|
|
|
I noticed in the main code that the coolant temperature variable is actually not even referenced... I never tested the function on cold engine, but I assume that it will work at any coolant temp. Be extra careful with something like that. There is more than one way for referencing stuff in the code, so even if there aren't any "direct" references, you better double-check. A good trick is to look for 16-bit var address directly in the hexdump, then check the code at whatever addresses you find. Just a totally random example: Say, we're looking for indirect pukor_w references, and we know that it is located at 0x38512A. So, take the 16-bit address (it should be 0x112A in this case) - and search your bin for it (mind the LoHi thing). Now, if you find something like "mov r12, 0x112Ah", treat it very carefully! Inspect the code, check DPPs, - and most likely it will actually be referencing your var.
|
|
|
Logged
|
|
|
|
TijnCU
Hero Member
   
Karma: +60/-4
Offline
Posts: 690
flying brick
|
 |
« Reply #136 on: November 21, 2016, 11:38:27 AM »
|
|
|
This is exactly how I relocated the variables (only in binary). They are quite easy to see in the launch control code block. I did some extra searching around the code call, but didnt find any references. I think it may be an error from the launchcontrol php script, because in my friends tt, the launch function also works at any operating temp. The launch control code is something different than full ecu code offcourse..
|
|
« Last Edit: November 21, 2016, 11:40:04 AM by TijnCU »
|
Logged
|
|
|
|
TijnCU
Hero Member
   
Karma: +60/-4
Offline
Posts: 690
flying brick
|
 |
« Reply #137 on: November 22, 2016, 09:45:12 AM »
|
|
|
Nice project! How are IAT's with this intercooler? I use same one, but heatexchange is quite bad. IAT's go high and water stays cold..
Hey Johan, I havent installed the intercooler yet. Have you played with pump speed? If you have too much water flow, it cant absorb all off the heat. In my case the water ic will be more efficient in any case since my intercoolers don't have direct airflow...(rear mounted)
|
|
|
Logged
|
|
|
|
turbojohan
Full Member
 
Karma: +5/-0
Offline
Posts: 185
|
 |
« Reply #138 on: November 22, 2016, 09:51:49 AM »
|
|
|
i run 600 hp with it so just need bigger core i think. But water stays really cool, maybe with less waterflow it will be better... But think i change to air/air. I use Golf 7 GTD pump.
|
|
|
Logged
|
|
|
|
TijnCU
Hero Member
   
Karma: +60/-4
Offline
Posts: 690
flying brick
|
 |
« Reply #139 on: November 22, 2016, 01:55:11 PM »
|
|
|
You could put a restrictor in the water exit and see if iats improve My setup with this engine will not be above 300hp for a road tune. Need to have low down power to move this 1750kg brick around  If I ever want to have more power, I will buy a larger engine.
|
|
|
Logged
|
|
|
|
turbojohan
Full Member
 
Karma: +5/-0
Offline
Posts: 185
|
 |
« Reply #140 on: November 22, 2016, 02:01:02 PM »
|
|
|
I have 830 kg car, no need for low end torque  Will try restrict waterflow. Seen quite some T3's with diesels, but never with 1.8t with 300 hp. Will turn quite some heads 
|
|
|
Logged
|
|
|
|
prj
|
 |
« Reply #141 on: November 23, 2016, 12:11:50 AM »
|
|
|
Water to air coolers should only be used where it is not possible to use a direct cooler. For example roots/screw blowers mounted on top of manifold, cars with rear-mounted engines and so on.
It is always much more efficient to go air->air than air->water->air.
|
|
|
Logged
|
|
|
|
TijnCU
Hero Member
   
Karma: +60/-4
Offline
Posts: 690
flying brick
|
 |
« Reply #142 on: December 09, 2016, 12:15:57 PM »
|
|
|
Combined powers from the launch function and the hard limiter  I need to do a proper video some day again, but this was just during my mapswitching test drive.. https://youtu.be/NVlC9XhhFwAIf I find the time to fix my loose shifter, next time I'll flat shift it into 2nd 
|
|
« Last Edit: December 09, 2016, 12:17:32 PM by TijnCU »
|
Logged
|
|
|
|
turbojohan
Full Member
 
Karma: +5/-0
Offline
Posts: 185
|
 |
« Reply #143 on: December 09, 2016, 01:19:41 PM »
|
|
|
LOL Never seen a T3 do that 
|
|
|
Logged
|
|
|
|
TijnCU
Hero Member
   
Karma: +60/-4
Offline
Posts: 690
flying brick
|
 |
« Reply #144 on: December 18, 2016, 05:39:09 AM »
|
|
|
I reworked my mapswitching completely, now every map gets switched from ram. Because I am now satisfied with both the automatic lpg mapswitching and the performance oriented mapswitching, I decided to take another look at switching an electric exhaust cutout. Because I am no expert in writing code, I decided to use a switched arduino instead. Here is what I did: I located the rear o2 sensor heater control in IDA. B_hshe is the bit for rear o2 heater on, so I followed that lead. I found that it sets P2.4, so I concluded that this must be the actual heater control. I placed NOP at the 3 locations where this pin is set, and implemented the bset P2.4 and bclr P2.4 in my mapswitching code. When I switch to the "performance map", ecu pin 63 starts to transmit a voltage (on other maps it gives out 0v). Then, the arduino receives this signal and is programmed to give 12v to one side of the exhaust motor (by use of 2 relays) for 2 seconds. The valve opens, and the arduino links both sides of the motor to ground. When I switch back to another map setting, the arduino gives 12v to the other side of the motor, reversing action. After 2 seconds it is both to ground again. Simple, but very cool function!  Total cost of arduino material: <10$ 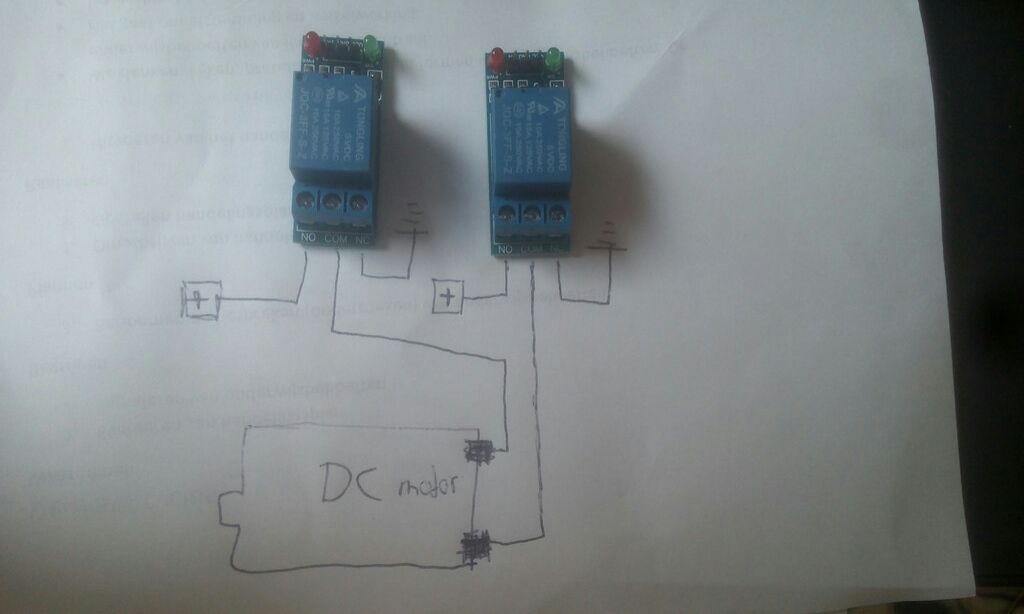
|
|
« Last Edit: December 18, 2016, 06:40:38 AM by TijnCU »
|
Logged
|
|
|
|
vwaudiguy
|
 |
« Reply #145 on: December 18, 2016, 01:52:58 PM »
|
|
|
Very cool idea. Just from experience, those electric exhaust cutouts usually live a short life, due to the conditions they work in. They tend to seize up over time.
|
|
|
Logged
|
"If you have a chinese turbo, that you are worried is going to blow up when you floor it, then LOL."
|
|
|
TijnCU
Hero Member
   
Karma: +60/-4
Offline
Posts: 690
flying brick
|
 |
« Reply #146 on: December 18, 2016, 02:00:36 PM »
|
|
|
Would you suggest to cycle the valve before every start? Its all stainless steel, and I mostly drive on lpg (very low carbon deposits). Might help with lifespan  The motor is very heavy too, same brushed dc motor as I have on my adjustable seats 
|
|
« Last Edit: December 18, 2016, 02:02:30 PM by TijnCU »
|
Logged
|
|
|
|
vwaudiguy
|
 |
« Reply #147 on: December 18, 2016, 03:03:13 PM »
|
|
|
Would you suggest to cycle the valve before every start? Its all stainless steel, and I mostly drive on lpg (very low carbon deposits). Might help with lifespan  The motor is very heavy too, same brushed dc motor as I have on my adjustable seats  I'm sure that would help. All the ones I've seen have the huge motors attached, and were also stainless. I see the OE VW ones for the TDI's seize up quite often as well. You would think that design would have been thought through/ optimized. 
|
|
|
Logged
|
"If you have a chinese turbo, that you are worried is going to blow up when you floor it, then LOL."
|
|
|
TijnCU
Hero Member
   
Karma: +60/-4
Offline
Posts: 690
flying brick
|
 |
« Reply #148 on: December 18, 2016, 03:47:42 PM »
|
|
|
Diesel is the other side of the scale when it comes to carbon deposits, but its good that you think with me! I have now programmed the arduino to cycle the valve once when I put the ignition on. I haven't built in the cutout yet, I will make it into a muffler first. I'll do some tests with different voltages first to see how it influences speed. Anyway, the whole point was to get rid of that stupid remote control  and make it a bit more integrated and intuitive. The durability will show in the time to come.... *one good thing about the cutout design is that it is a worm gear setup, so there is no way the exhaust gas can control the valve + lots of torque from the motor. Test on the bench: https://www.youtube.com/watch?v=j-QDCXax4IYAdded arduino tvout for display on my multimedia radio in the car. Ordered 2 more thermocouples to monitor intercooler coolant temp and post cooler temp  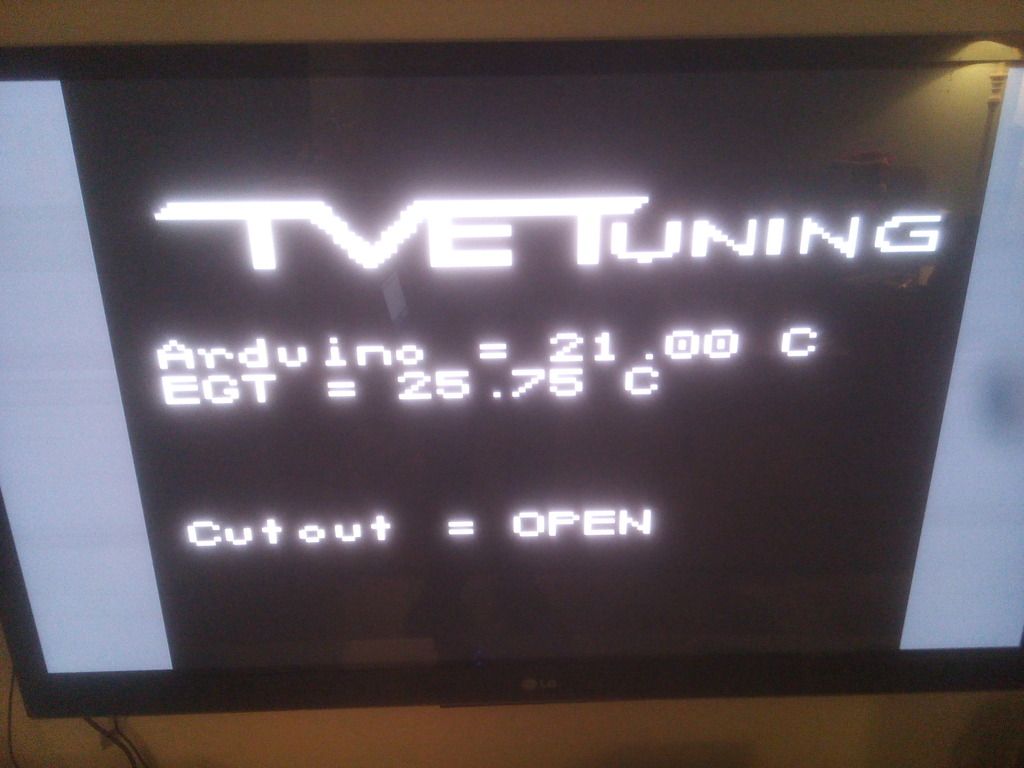
|
|
« Last Edit: December 22, 2016, 02:44:59 PM by TijnCU »
|
Logged
|
|
|
|
prj
|
 |
« Reply #149 on: January 29, 2017, 07:02:38 AM »
|
|
|
The only cutouts that work well in my experience are Pierburg. The ones used by OEM's. You can buy them in vacuum and electronic form in quite a few different shapes and sizes.
The only downside is the prices start at about ca. 150-200 EUR for one cutout.
I have used mostly vacuum ones. On a B5 RS4 we blocked one tail pipe hole, and it made the exhaust a lot more quiet cruising and idle. I used the N335 flap control map to control it from the ECU.
On a Porsche Cayenne Hybrid 3.0 TFSi who needed more sound we welded bypass pipes with flaps to the original exhaust, bypassing the big rear silencer. Here the best and smooth results were by using simply the vacuum from the intake manifold (they are closed under vacuum). This made for a smooth transition, having the car quiet at low rpm's and low load, and the exhaust really coming alive at WOT.
|
|
|
Logged
|
|
|
|
|