A6_C5_Allroad
Full Member
 
Karma: +0/-0
Offline
Posts: 116
|
 |
« Reply #30 on: April 01, 2014, 05:06:13 PM »
|
|
|
I just spoke with a tech at Coolingmist and I am told that any 0-5v supply is ok to use with the Vari-Cool 2 controller. Although, he couldn't give me an idea of how to do this using injector duty cycle. If it's just a matter of tapping into one of the injector signal wires and grnd., then I guess that I should be ok.
|
|
|
Logged
|
|
|
|
julex
|
 |
« Reply #31 on: April 02, 2014, 08:19:38 AM »
|
|
|
I just spoke with a tech at Coolingmist and I am told that any 0-5v supply is ok to use with the Vari-Cool 2 controller. Although, he couldn't give me an idea of how to do this using injector duty cycle. If it's just a matter of tapping into one of the injector signal wires and grnd., then I guess that I should be ok.
Problem is injectors are supplied 12V signal and in its nature it is a PWM signal off-on-off. So at a minimum you need a 5V voltage regulator to bring input voltage to 5V. Luckily these days it is just one transistor looking like component that can take anything from 6v to 40V and regulate it to 5V (it supports up to 1.5A so much more than we need). This would be our basic signal, it would still be PWM though... Now, hooking that up might just be enough. WM controllers are nothing else than analog to PWM signal converters with adjustable "duty cycle". WM pump take flat 12V and WM controller controls the on-off-on frequency which results in pump working anywhere from (usually) 15% to 100% of time. Feeding the 5V from our voltage converter and supplying it to WM controller might be all we need here... however he problem is that with large enough injectors where duty cycle never reaches high % (like mine which reaches top 65%-70%), the signal might not be adequate as I wouldn't be able to run system at 100% ever which would have its drawbacks (poor atomization due to low pressure if I cannot run pump 100% at peak). Sorry for long post.
|
|
|
Logged
|
|
|
|
A6_C5_Allroad
Full Member
 
Karma: +0/-0
Offline
Posts: 116
|
 |
« Reply #32 on: April 02, 2014, 10:29:58 AM »
|
|
|
Problem is injectors are supplied 12V signal and in its nature it is a PWM signal off-on-off. So at a minimum you need a 5V voltage regulator to bring input voltage to 5V. Luckily these days it is just one transistor looking like component that can take anything from 6v to 40V and regulate it to 5V (it supports up to 1.5A so much more than we need). This would be our basic signal, it would still be PWM though...
Now, hooking that up might just be enough. WM controllers are nothing else than analog to PWM signal converters with adjustable "duty cycle". WM pump take flat 12V and WM controller controls the on-off-on frequency which results in pump working anywhere from (usually) 15% to 100% of time. Feeding the 5V from our voltage converter and supplying it to WM controller might be all we need here... however he problem is that with large enough injectors where duty cycle never reaches high % (like mine which reaches top 65%-70%), the signal might not be adequate as I wouldn't be able to run system at 100% ever which would have its drawbacks (poor atomization due to low pressure if I cannot run pump 100% at peak).
Sorry for long post.
I follow what you are saying. Wouldn't there be a way that you could compensate for the 65%-70% duty cycle limit? It appears as though you have some really good understanding of electronics, so maybe designing something that would see the 65% duty cycle as 100% duty cycle, yet exponentially scaled back the lower the duty cycle, would achieve the goal??? I think that using Injector Duty Cycle is such a novel and logical idea and certainly warrants further investigation. It just makes complete sense to me, to use the demand for fuel as the same demand for the W/M injection to condense that fuel.
|
|
|
Logged
|
|
|
|
julex
|
 |
« Reply #33 on: April 03, 2014, 07:31:44 AM »
|
|
|
I follow what you are saying. Wouldn't there be a way that you could compensate for the 65%-70% duty cycle limit? It appears as though you have some really good understanding of electronics, so maybe designing something that would see the 65% duty cycle as 100% duty cycle, yet exponentially scaled back the lower the duty cycle, would achieve the goal??? I think that using Injector Duty Cycle is such a novel and logical idea and certainly warrants further investigation. It just makes complete sense to me, to use the demand for fuel as the same demand for the W/M injection to condense that fuel.
When I get some time I will put together a simple RC filter that will convert 12V PWM to "good enough" 0-5V analog signal. It should be true 0-100% converter, no 12V will mean 0V out and it will linearly go up to 5V as 12V input duty reaches 100%. Once that's done, the WM controller can be set up via both potentiometers to activate with certain level of voltage input and go full blast at whatever would the max injector duty cycle result at that 0-5V scale. This is nothing new though, I know at least of two WM systems that can take injector DC signal in and properly inject WM in.
|
|
|
Logged
|
|
|
|
A6_C5_Allroad
Full Member
 
Karma: +0/-0
Offline
Posts: 116
|
 |
« Reply #34 on: April 03, 2014, 01:39:29 PM »
|
|
|
When I get some time I will put together a simple RC filter that will convert 12V PWM to "good enough" 0-5V analog signal. It should be true 0-100% converter, no 12V will mean 0V out and it will linearly go up to 5V as 12V input duty reaches 100%.
Once that's done, the WM controller can be set up via both potentiometers to activate with certain level of voltage input and go full blast at whatever would the max injector duty cycle result at that 0-5V scale.
This is nothing new though, I know at least of two WM systems that can take injector DC signal in and properly inject WM in.
I follow what you are saying. I heard from someone today that tells me that the Labonte W/M Progresive Contoller has the hardware and software to convert Injector Duty Cycle into analog 0-5v, very linear. But I'll bet the damn thing costs over $1k, or close. I like your plan. When you're done, I hope that you can spare, or even sell your plans to me for to build the RC Filter that converts 12v PWM to 0-5v analog. The CMSG ( Contoller ) that I am currently using, allows for a combination of boost PSI & 0-5V supply. I don't quite understand it yet, but hopefully will by the time you have your converter planned & built.
|
|
|
Logged
|
|
|
|
jjpetek
Newbie
Karma: +0/-0
Offline
Posts: 2
|
 |
« Reply #35 on: October 29, 2022, 09:26:15 AM »
|
|
|
Hi, here an idea to control a water methanol injection by using the "intake air changeover function" on the original RS4 551K ECU.  The RS4 551K ECU has an implemented function to control the airbox flap. I have blocked my open airbox flap, so I can use this function to control a pump for a water methanol injection. To do this, I will disconnect the harness connector from the N335 and plug it into a relay to switch a electrical high-pressure water pump. The N335 is connected to pin 44 of the 551K ECU. There are 2 values and 1 map to control it: KFLUKL [load/RPM] at hex 1A906 "Kennfeld zur Steuerung der Luftfilterklappe" TLUKL [sec] at hex 1A946 "Verzögerungszeit für Schließen der Luftfilterklappe" and VLUKL [km/h] at hex 1A947 "vfzg - Schwelle für Öffnen der Luftfilterklappe" With this info we can control a pump by KFLUKL over load and RPM with a vehicle speed threshold. I will do this in the next month, because I don't have time at the moment. The "intake air changeover function" is not documented in the ME7.1 Funtionsrahmen, because it is a special function only in the RS4. N335 is Pin 105 N112 is Pin 44 This is illustrated in the wiring diagram and verified using output tests with VCDS. This function being rpm/load switched is also very useful for activating a 2nd fuel pump as opposed to a hobbs switch or other less elegant technique. It's a pull to ground signal.
|
|
|
Logged
|
|
|
|
BlackT
|
 |
« Reply #36 on: November 02, 2022, 12:05:30 PM »
|
|
|
How to activate pin 105 on other ECUs?
Or any other output directly? How that look in ASM?
Let say if I put B_mill to 1 it will activate output on pin for MIL light. But I think that B_mil somewhere on other place tell ECU to put that pin to ground?
|
|
|
Logged
|
|
|
|
fknbrkn
Hero Member
   
Karma: +185/-23
Offline
Posts: 1454
mk4 1.8T AUM
|
 |
« Reply #37 on: November 02, 2022, 12:18:26 PM »
|
|
|
How to activate pin 105 on other ECUs?
Or any other output directly? How that look in ASM?
Let say if I put B_mill to 1 it will activate output on pin for MIL light. But I think that B_mil somewhere on other place tell ECU to put that pin to ground?
B_mil is a canbus bit so its just iram adr (typically its something like 0xF8xx) Final point in asm for cpu ports looks like 'bclr p6_4' iirc read c167um for port control
|
|
|
Logged
|
|
|
|
BlackT
|
 |
« Reply #38 on: November 02, 2022, 01:25:26 PM »
|
|
|
Thank you very much I think I got it
pin 105 is connected to port P0.0
PS: I am not sure will this set this port to HIGH/LOW or will it change its function, I must go tru FR couple times to see what this does
Also this P0.0 is not at C167 procesor is labeled as CC650_1
|
|
« Last Edit: November 02, 2022, 01:35:03 PM by BlackT »
|
Logged
|
|
|
|
prj
|
 |
« Reply #39 on: November 02, 2022, 03:06:29 PM »
|
|
|
Just use 551K for everything. There is no reason to use anything else...
|
|
|
Logged
|
|
|
|
BlackT
|
 |
« Reply #40 on: November 02, 2022, 11:27:07 PM »
|
|
|
What about when I want to use this on 1.8T? Pin 114 is free let's say
And also I am planing to put in my car M7.1.1 ECU beacuse I have 6hp gearbox instaled.
So croshflashing to 551K is not option
|
|
« Last Edit: November 03, 2022, 01:20:48 AM by BlackT »
|
Logged
|
|
|
|
BlackT
|
 |
« Reply #41 on: November 03, 2022, 07:58:19 AM »
|
|
|
Let's go back to M7.1 from 2.7TT PIN 105 on ECU connector is connected to CJ920 2/3 OUTPUT
That is input pin 10 on CJ920 and it goes to MCU pin 47 P2.0 Now, problem is M7.1 have two MCUs, how in flash we know witch one we control?
|
|
|
Logged
|
|
|
|
flamy
Full Member
 
Karma: +6/-0
Offline
Posts: 56
|
 |
« Reply #42 on: November 03, 2022, 08:57:14 AM »
|
|
|
Let's go back to M7.1 from 2.7TT PIN 105 on ECU connector is connected to CJ920 2/3 OUTPUT
That is input pin 10 on CJ920 and it goes to MCU pin 47 P2.0 Now, problem is M7.1 have two MCUs, how in flash we know witch one we control?
The LUV is connected to P2.0 of the ASIC. Thus it is controlled via SSC interface between CPU and ASIC. You have to figure out at which address the according communication register for controlling the state of this pin is. Edit: Looked a few minutes on it by myself. Searching for occurrences of TLUKL (0x81A946) leads to position of "intake air changeover function" at 0x8A3BB0. Evaluating this function shows usage of RAM-address 0x380CB7. Looking for XREFs on this address shows usage of it in function placed at 0x870888. Due to some own researches, I know that this function handles the communication between CPU and ASIC using "0xFDE?" registers. CODE3:870A60 loc_870A60: ; CODE XREF: sub_870888+1CC↑j CODE3:870A60 C2 F4 B7 8C movbz r4, byte_380CB7 CODE3:870A64 68 41 and r4, #1 CODE3:870A66 2D 02 jmpr cc_Z, loc_870A6C CODE3:870A68 6F 88 bset USR0 CODE3:870A6A 0D 01 jmpr cc_UC, loc_870A6E CODE3:870A6C ; --------------------------------------------------------------------------- CODE3:870A6C CODE3:870A6C loc_870A6C: ; CODE XREF: sub_870888+1DE↑j CODE3:870A6C 6E 88 bclr USR0 CODE3:870A6E CODE3:870A6E loc_870A6E: ; CODE XREF: sub_870888+1E2↑j CODE3:870A6E 3A 88 74 60 bmovn word_FDE8.0, USR0 Looking at this piece of code, my assumption is that 0xFDE8.0 is used to transmit the level of the output pin P2.0 for the LUV to the ASIC.
|
|
« Last Edit: November 03, 2022, 12:03:48 PM by flamy »
|
Logged
|
|
|
|
BlackT
|
 |
« Reply #43 on: November 03, 2022, 04:13:48 PM »
|
|
|
Thank you very much  , now I have something to work with it. I will do some test and post results here
|
|
|
Logged
|
|
|
|
BlackT
|
 |
« Reply #44 on: November 04, 2022, 11:15:56 AM »
|
|
|
I didn't get far When 0xFDE8.0 is 1, pin P2.0 is HIGH, and relay on pin 105 is not activated I try to force FDE8.0 to zero but without success I have change this two bset to bclr, but looking in me7looger FDE8.0 is still 1 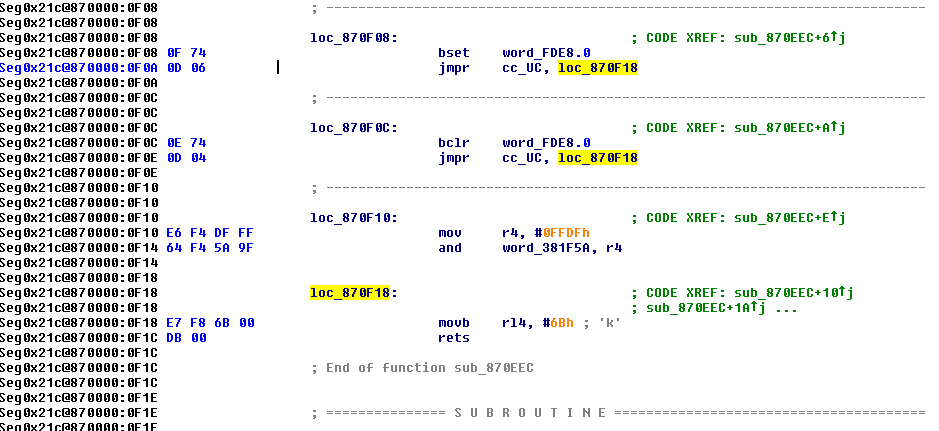 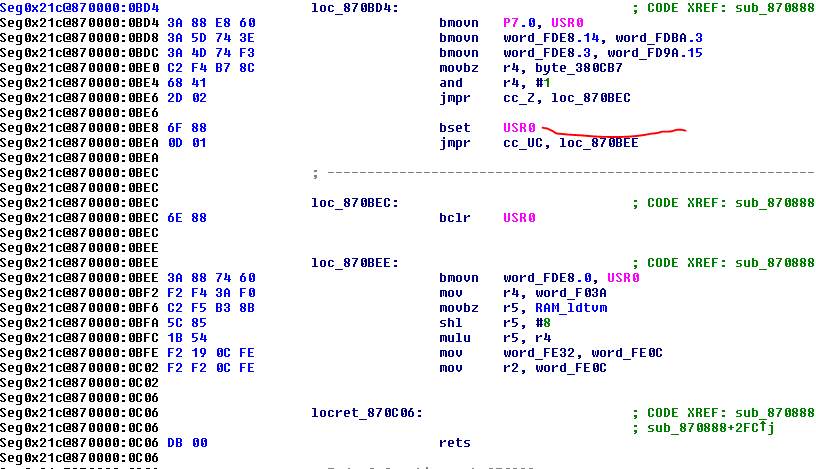 When I set whole KFLUKL to 2, I get 0 on FDE8.0 above 50 kmh, and relay on 105 get activated Also when I upload other file( for example 4Z7 D) FDE8.0 is zero, but P2.0 is still HIGH I need to dig more
|
|
|
Logged
|
|
|
|
|